CHRISTMAS: BROUGHT TO YOU BY CHINESE SLAVE LABOR

Beyblade spinning tops, Zhu Zhu Pets and remote-controlled Cars 2 cars are this year’s star Christmas toys. But behind the scenes little Christmas cheer surrounds the production of these toys, in an industry that’s worth $80 billion a year globally. Now a report on working conditions in the toy industry in China has comes down hard on industry leaders Disney and Mattel.
Between May and October, which represents the busy season for toy factories, a group of academics based in Hong Kong, Sacom, and the organization China Labor Watch (CLW) conducted a thorough investigation into several sub-contractors of these multinationals.
Wages paid late, mandatory overtime, denial of rest days, the prohibiting of talking or going to the toilet, punitive fines, sexual discrimination, harassment: the investigation reveals an impressive list of abuses and violations of basic rights.
Three Barbies sold every second
The toy industry in China employs four million workers who produce 80% of the toys sold worldwide, and 90% of the toys imported into Europe. 4,000 Chinese factories work for subcontractors of Mattel and Disney. 70% of these factories are located near the coast of southern China, in the delta of the Pearl River. This area is regarded as a “special economic zone”, a sort of hinterland of Hong Kong.

Back in 2001, a report by the Hong Kong Christian Industrial Committee (HKCIC) denounced the “hellish” working conditions there, pointing the figure of blame squarely at Hasbro, McDonald’s, Disney and Mattel. “Ten years later, nothing has really changed, despite some minor improvements,” laments Debby Chan, project manager at Sacom.
Each year, the world’s leading toy manufacturer Mattel sells millions of Barbie dolls (three per second), 80% of which are made in China. At Sturdy Products in Shenzhen, they manufacture Hot Wheels toy cars. At this factory, denounced by Sacom in 2007, some 6,000 workers work flat out, 12 hours a day, six days a week, for staggeringly low wages. According to Sacom:
Wages are kept at extremely low levels, due to production quotas that are almost impossible to complete.
At the factory, which in 2010 exported more than $30 million worth of toys, the workers receive €154 per month, the minimum wage. By working overtime they can expect to reach €327 each month. To achieve this, the legal maximum of 36 hours overtime per month is regularly exceeded. Last summer employees of Sturdy Products worked between 100 and 120 hours of overtime per month, as evidenced by payroll receipts obtained by Sacom.
Some workers claim they were pressured when they were initially hired to sign a document committing them to work beyond the legal overtime maximum. Debby Chan of Sacom describes “undignified” working conditions that are close to “hell”:
The workers, mostly women, are constantly harassed and insulted by their bosses. Production quota are excessive, they require them to produce a lot in a short time. There is serious negligence in terms of health and safety. The workers use hazardous chemical products, thinners, adhesives, lead. Surgical masks are provided to them, but they are ineffective in protecting them from toxic fumes. Recently, two workers had to be hospitalized, but have received no compensation from their employers.
According to the NGO’s survey, the Shenzhen factory employed many children between the ages of 14 and 15. In May 2011, Nianzhen Hu, a factory worker, committed suicide by jumping from the sixth floor of the factory. According to her family, she was often “reprimanded” by management “because she was not efficient enough”. She had been ordered, as punishment, not to come to work.
Ineffective audits
Since 2006, the plant has regularly received a “seal of compliance” from the International Council of Toy Industries (ICTI). For ten years, the ICTI has conducted social audits of over 2,400 Chinese factories. Designed to “promote ethical manufacturing”, the “care process” of the ICTI is based on a “code of business practices” imposed on subcontractors to multinational members, such as Mattel, which prohibits child labor and issues a series of “rules of good conduct” to be respected: “a safe working environment”, “emergency medical assistance”, sick leave, etc..
Marie-Claude Hessler, a former lawyer for Amnesty International, is a minority shareholder of Mattel. She views the audits of the ICTI as “smoke and mirrors.”
Inspectors from the ICTI come from Europe or the United States, without any real knowledge of the local environment. They are very easy to fool. And when the Federation uses external audit companies, factories regularly complain about the corruption of inspectors, who they claim demand money in return for a seal of compliance.
Feng Yu, 21, spent three years working in a number of toy factories in Shenzhen. “Before the inspections, we would gather in a room, and they would explain to us the questions that they would ask us, and especially what to reply to the inspectors.” At Sturdy Products, Sacom has even reported cases of workers being paid to lie during audits. Debby Chan is under no illusion:
In reality, factory managers are informed in advance of the arrival of the inspectors, so they have time to do some spring cleaning – to hide the chemical products, to send home the children, to manufacture some fake employment contracts and false pay slips. It’s all a production that is set up to deceive the inspectors.
Ms. Hessler deplores the attitude of Mattel and other toy giants such as Disney, who “rely more and more on ICTI audits, instead of conducting their own audits.” In 1997, Mattel set up a unit of independent experts, who visited factories every three years, enforcing the code of conduct of the company. “At the time, the company had a CEO who was a bit ahead of his time, but since he has been replaced, Mattel has disbanded this independent commission and hidden behind the ICTI, confining themselves to publishing the reports of the Federation from time to time,” adds Marie-Claude Hessler. “For the toy industry, audits will continue to remain ineffective..the benefits are too great.”

Questioned by OWNI, the president of the ICTI, Christian Ewert, rejects this description. “The purpose of our code of business practices is to ensure fair treatment of workers in toy factories around the world. When a factory does not adhere to the code, we ensure that it fixes the problem. Our inspections are of a high quality.” He fires back at Sacom:
Sacom is really not open to the ICTI Care Process. In recent years it has continued to criticize us, never giving us credit for our actions, and refusing to meet us. We are open to dialogue, however. We accept the investigations of NGO’s, and act as soon as the results of these investigations are communicated to us, or when a worker contacts usto complain about their factory. Our work takes place over time, it takes time, and every year things are getting better and better.
30 hours of uninterrupted work
Also singled out in the report are the Walt Disney Company. At Sturdy Products, the Chinese workers produce the popular Lightning McQueen toy, hero of the film Cars. In its latest report, Sacom also examines the situation at On Tai Toys and Hung Hing Printing, two factories nestled in the delta of the Pearl River. Every winter these factories produce Buzz Lightyear action figures and Disney coloring books, while workers endure 12 to 14 hour days in dangerous conditions.
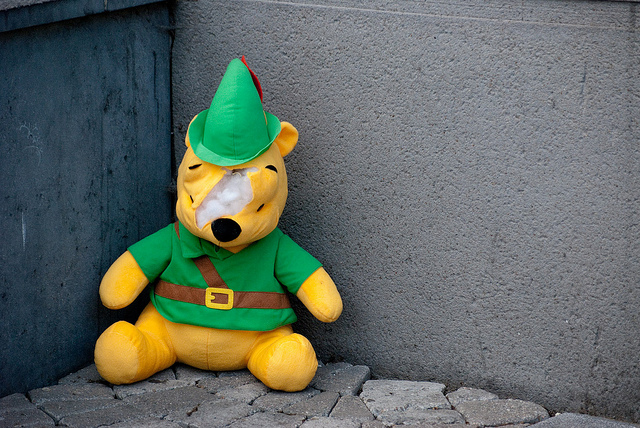
In the factory of Tai Toys, workers handle poorly labeled chemical products without the correct protective gloves or masks. They sleep in the factory, in tiny dormitories overrun by rats and insects. €40 is deducted from workers’ wages each month to cover meals and board. At Hung Hing injuries are common, and wages are often paid three weeks or a month late.
OWNI contacted the various factories which are the focus of the report. At On Tai Toys, “we do not respond to reporters,” was the sober response of a factory manager. At Sturdy Products, Damon Chan, one of the managers of the factory, requested some time before answering (OWNI is still waiting for his answer), but indicated that “Sturdy Products take this case very seriously.”
The only real reaction came from the Director General of the Hung Hing Printing Group, Dennis Wong. He justified exceeding the legal limits on overtime because the basic wages of workers “are not enough to live on.” According to him “the workers can not earn more than 154 euros a month, so they need those extra hours.” Between June and October, during the peak season, employees at Hung Hing worked up to 100 hours a month, some working up to 30 uninterrupted hours, simply to “fulfill an order deadline.”
No comments:
Post a Comment
Comments always welcome!